What is the range of fabric weights and thicknesses that can be achieved with spunbond nonwoven?
The range of fabric weights and thicknesses that can be achieved with spunbond nonwoven can vary depending on several factors, including the specific production process, the choice of raw materials, and the machinery used.
Here’s a general overview of the potential range:
Fabric Weight (Basis Weight):
- Lightweight Spunbond: Lightweight spunbond nonwovens can have a basis weight as low as 10 grams per square meter (gsm) or even lower. These are often used in applications where a thin and lightweight material is required, such as disposable medical gowns or hygiene products.
- Medium Weight Spunbond: Spunbond nonwovens with medium weights typically range from 15 gsm to 70 gsm. They are versatile and find use in various applications, including agriculture, packaging, and protective clothing.
- Heavyweight Spunbond: Heavyweight spunbond nonwovens can have basis weights exceeding 70 gsm. These are employed in applications where strength, durability, and barrier properties are essential, such as construction, geotextiles, and industrial packaging.
Fabric Thickness:
- Thin Spunbond: The thickness of a spunbond nonwoven fabric is generally related to its basis weight. Thin spunbond nonwovens can have a thickness of less than 0.1 millimeters (mm). These thin materials are often used in applications that require flexibility and minimal bulk.
- Medium Thickness Spunbond: Spunbond nonwovens with medium thickness typically range from 0.1 mm to 0.3 mm. They offer a balance between strength and flexibility, making them suitable for a wide range of applications.
- Thick Spunbond: Thick spunbond nonwovens, with a thickness exceeding 0.3 mm, are employed in applications that require cushioning, impact resistance, and insulation properties. They are used in various industrial and construction applications.
It’s important to note that the achievable fabric weights and thicknesses depend on the specific production process and the machinery used. Manufacturers can adjust machine settings, such as line speed and polymer throughput, to control the basis weight and thickness of spunbond nonwovens to meet the requirements of their target products and industries. The choice of raw materials and additives can also impact the final properties of the spunbond nonwoven, including its weight and thickness.
How do the spinning and bonding processes in spunbond nonwoven machinery work to create a cohesive fabric from thermoplastic polymer fibers?
The production of spunbond nonwoven fabric involves two primary processes: spinning and bonding. These processes work together to create a cohesive fabric from thermoplastic polymer fibers.
Here’s how they operate:
Spinning Process:
- Extrusion: The process begins with the extrusion of thermoplastic polymer pellets. These polymers are typically polypropylene (PP) or polyethylene (PE), although other polymers can be used. The polymer pellets are melted in an extruder, creating a molten polymer.
- Filament Formation: The molten polymer is then forced through a spinneret, which is a specialized nozzle with multiple small holes. China spunbond non woven As the polymer exits the spinneret, it is rapidly cooled and solidifies, forming continuous filaments. The number of holes in the spinneret and the polymer throughput determine the filament density.
- Web Formation: The filaments are drawn onto a moving conveyor belt or drum, where they are deposited in a random or controlled manner, creating a web of filaments. This web is known as the “spunbond web.”
Bonding Process:
- Thermal Bonding: In thermal bonding, the spunbond web passes through heated calender rolls or a heated oven. The heat softens the thermoplastic filaments, causing them to fuse together at contact points. The pressure applied by the calender rolls further bonds the filaments, creating a cohesive nonwoven fabric.
- Calendering: Calender rolls can have different patterns and surface textures, allowing for the creation of various nonwoven fabric designs. The choice of calender roll and its temperature can influence the fabric’s final properties.
- Cooling and Winding: After thermal bonding, the fabric is cooled and then wound onto rolls for further processing or conversion into rolls of nonwoven fabric.
It’s important to note that the bonding process in spunbond nonwoven machinery creates a fabric with a characteristic “spunbond” appearance, featuring a random arrangement of filaments with distinct thermal bonding points.
The result is a nonwoven fabric with properties such as strength, breathability, and dimensional stability, making it suitable for various applications, including hygiene products, agriculture, packaging, and geotextiles. The choice of polymer type, filament density, bonding method, and additives can further customize the fabric’s properties to meet specific industry and application requirements.
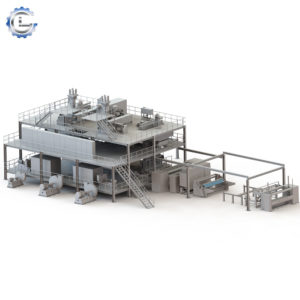