What are the advantages of using high-quality track rollers?
Using high-quality track rollers in an excavator can offer several advantages, including:
Durability and Longevity: High-quality track rollers are designed to withstand the demanding conditions of excavator operation. They are made from robust materials and undergo rigorous manufacturing processes to ensure durability and longevity. This means that they are less likely to wear out prematurely or fail under normal operating conditions, reducing the frequency of replacements and associated downtime.
Enhanced Performance: High-quality track rollers can contribute to improved machine performance. They provide smooth and efficient movement of the tracks, reducing friction and resistance. This can result in better traction, increased maneuverability, and enhanced overall productivity of the excavator.
Reduced Maintenance and Repair Costs: Using high-quality track rollers can help minimize maintenance and repair costs. They are less prone to premature wear, damage, or failure, reducing the frequency of repairs and replacements. This translates into lower maintenance expenses and less downtime for the excavator, resulting in improved cost-effectiveness.
Optimal Fuel Efficiency: High-quality track rollers, along with other undercarriage components, can contribute to optimal fuel efficiency. They help reduce friction and rolling resistance, allowing the engine to operate more efficiently. Improved fuel efficiency can result in cost savings over the long term, especially for excavators that are frequently operated.
Minimized Damage to Ground and Surfaces: High-quality track rollers, designed with appropriate dimensions and materials, help distribute the weight of the excavator over a larger surface area. This reduces ground pressure and minimizes damage to sensitive surfaces, such as grass, asphalt, or delicate terrains. It helps preserve the integrity of the ground and minimizes the need for costly repairs or restoration.
Compatibility and Reliability: High-quality track rollers are specifically designed to fit and function seamlessly within the excavator’s undercarriage system. They are engineered to meet or exceed OEM specifications, ensuring compatibility and reliable performance. Using track rollers from reputable manufacturers offers peace of mind, knowing that the components are designed to meet the highest quality standards.
It is important to note that the advantages of high-quality track rollers are not limited to the rollers alone. They can also positively impact the performance and lifespan of other undercarriage components, such as sprockets, idlers, and track links, mini excavator track rollers as they work together as a system. Therefore, investing in high-quality track rollers can have broader benefits for the overall performance, reliability, and cost-effectiveness of the excavator.
How do you determine the correct track roller size and configuration for an excavator?
Determining the correct track roller size and configuration for an excavator involves considering several factors. Here are the key steps to help you determine the appropriate track roller size and configuration:
Consult the Manufacturer’s Documentation: Start by referring to the excavator’s manufacturer documentation, such as the user manual, parts catalog, or specifications sheet. These resources often provide detailed information about the recommended track roller size, configuration, and specifications for each specific excavator model.
Identify the Excavator Model and Undercarriage Type: Determine the exact model and brand of the excavator, as well as the undercarriage type. Undercarriage types can vary, such as standard, long reach, heavy-duty, or low ground pressure. This information is important as it helps in identifying the appropriate track roller options compatible with the specific undercarriage configuration.
Consider Machine Weight and Application: Take into account the weight of the excavator and the nature of the application it will be used for. Different track roller configurations may be recommended based on the weight of the machine and the anticipated load-bearing requirements. For example, heavy-duty applications may require track rollers with higher load capacities.
Evaluate Track Roller Dimensions: Review the dimensions of the existing track rollers or the manufacturer’s specifications to determine the appropriate size for replacements. Pay attention to the diameter, width, and overall dimensions of the track rollers. Ensuring compatibility with the undercarriage system is crucial, so the new track rollers fit properly and function effectively.
Consider Operating Conditions: Evaluate the operating conditions in which the excavator will be used. Factors such as terrain type, ground conditions, climate, and application-specific requirements may influence the choice of track roller configuration. For example, if the excavator will be operating on rocky or abrasive terrain, track rollers designed for such conditions may be preferable.
Seek Expert Advice: If you are uncertain or need assistance with determining the correct track roller size and configuration, it is advisable to consult with authorized dealers, service technicians, or experts who have experience with the specific excavator model. They can provide valuable guidance based on their expertise and knowledge of the equipment.
Remember that track rollers are an integral part of the excavator’s undercarriage system, and selecting the correct size and configuration is crucial for optimal performance, durability, and safety. It is recommended to rely on the manufacturer’s recommendations and seek professional advice when necessary to ensure the right track rollers are chosen for the excavator.
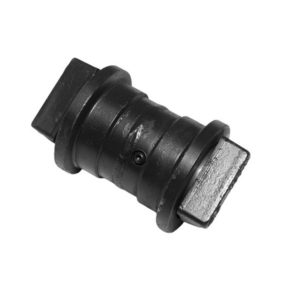