How is the galvanizing process monitored to maintain consistency and quality in finished products?
Monitoring the galvanizing process is crucial to maintaining consistency and quality in finished products. Here’s how it is typically done:
- Pre-Galvanizing Inspection: Before the galvanizing process begins, the material to be galvanized undergoes thorough inspection. This includes checking for surface contaminants, such as rust, oil, or grease, which can affect the quality of the galvanized coating. Any surface defects or irregularities are addressed before proceeding with galvanizing.
- Bath Chemistry Control: The chemical composition of the galvanizing bath is continuously monitored and controlled to ensure it remains within specified parameters. This includes monitoring the concentrations of zinc, fluxes, and other additives in the bath to maintain proper galvanizing conditions. Regular chemical analysis of the bath solution is conducted to verify its composition and adjust as necessary.
- Temperature Control: The temperature of the galvanizing bath is closely monitored and controlled to maintain the optimal operating range for the galvanizing process. Temperature fluctuations can affect the quality and appearance of the galvanized coating, so precise temperature control is essential.
- Bath Maintenance: The galvanizing bath is regularly maintained to remove impurities, dross, and other contaminants that can accumulate during the galvanizing process. This includes skimming the surface of the bath to remove dross, as well as periodic cleaning and maintenance of the bath equipment.
- Visual Inspection: Visual inspection of the galvanized coating is conducted throughout the process to detect any defects or irregularities. galvanized fittings This includes inspecting the surface of the material before and after galvanizing, as well as examining the finished products for uniformity, adherence, and overall quality of the coating.
- Thickness Measurement: The thickness of the galvanized coating is measured at regular intervals to ensure it meets specified requirements. Non-destructive thickness measurement techniques, such as magnetic or eddy current methods, are commonly used to assess coating thickness accurately.
- Adhesion Testing: Adhesion testing is performed to evaluate the bond strength between the galvanized coating and the substrate material. Various methods, such as tape adhesion tests or scratch tests, may be used to assess the integrity of the coating and ensure it adheres properly to the substrate.
- Quality Control Checks: Quality control checks are conducted at key stages of the galvanizing process to verify that all process parameters are being met and that the finished products meet required quality standards. This may include dimensional checks, visual inspections, and testing for coating thickness and adhesion.
- Documentation and Record-Keeping: Comprehensive documentation and record-keeping are maintained throughout the galvanizing process to track process parameters, test results, and any deviations from established procedures. This documentation provides traceability and accountability and facilitates continuous process improvement.
By implementing these monitoring and control measures, galvanizing facilities can ensure consistency and quality in finished products, resulting in durable and corrosion-resistant coatings that meet the requirements of various applications.
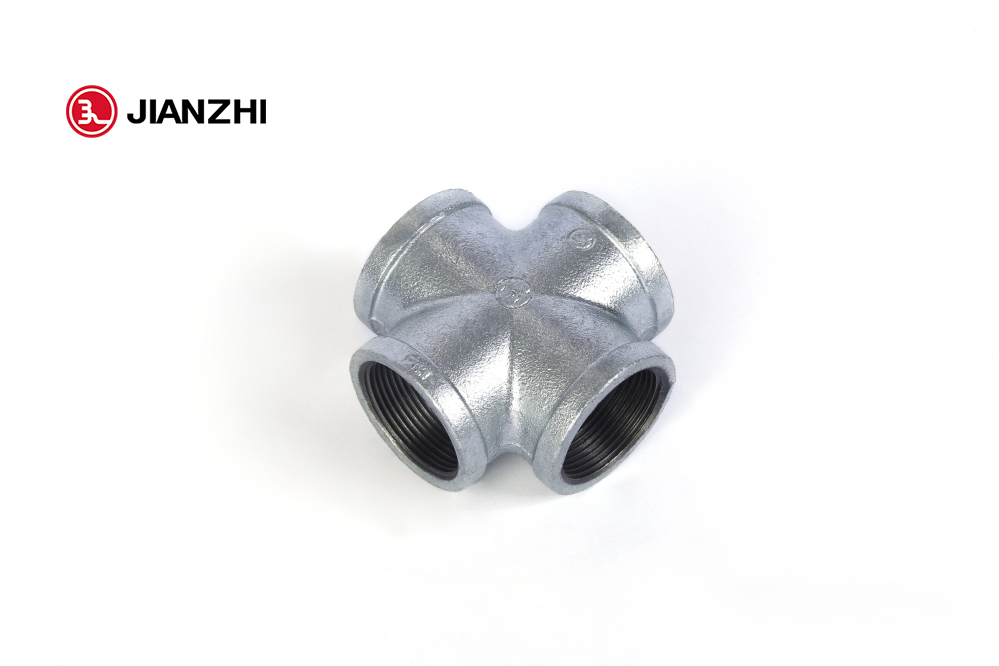